QMS Implementation
QMS Implementation
Put your trust in us
At 8C Healthcare, we understand that ‘quality’ applies to the whole organization and there by goes beyond the product itself. Hence building a pertinent QMS, implementing it and confirming continuous improvements throughout the product lifecycle is significant.
A medical device quality management system is an organised system of processes, procedures and resources required to develop high quality products, achieve quality objectives and satisfy customer needs. We help our clients find the right sized QMS and we understand that every company has different needs depending on their stage of product development and business goals.
We understand that a critical part of regulatory compliance in major markets is the establishment of a quality management system. We help our clients to build and implement a full quality management system that is in compliance to medical device regulations and standards i.e., Quality System Regulation and ISO 13485. By using our expertise, we work with our clients to even develop compliant technical documentation.
The services we offer are:
- Gap assessment of Client QMS
- Developing QMS strategy by determining regulatory strategies for your markets of interest
- QMS Set-up and implementation by providing customized templates and forms.
- Including ISO 13485, MDSAP, QSR requirements into the scope of the QMS
- Necessary training on QMS, Risk Management, Design Controls.
- Risk Management Support
- DHF Assessment and Remediation
- Auditing of the existing QMS, prior to certification audit.
- Assisting management by finding a Notified Body for external auditing and certification
- Obtaining successful ISO 13485 certification
ISO 13485:2016
ISO 13485 is a harmonized standard that lists the requirements that are intended to be applicable to any medical device organization as a basis for illustrating and supporting their compliance to applicable regulatory requirements. A QMS that is in accordance with ISO 13485 requirements is a documented set of interrelated processes, including forms or templates, that establish, implement, and maintain the provisions outlined in the requirements of the standard with the aim of meeting customer and regulatory requirements.
ISO 13485 provides a framework for good management practice that can be applied at the organization. Requirements of ISO 13485:2016 are applicable to organizations irrespective of their size and regardless of their type. Wherever requirements are specified as applying to medical devices, the requirements apply equally to associated services, supplied by the organization. ISO 13485 contains requirements for improvement, utilizing feedback from sources such as complaint handling, post market surveillance, handling of nonconformities, corrective actions and preventive actions.
FDA QSR
The quality system regulation establishes a framework to be followed by medical device manufacturers and provides them greater flexibility in achieving quality requirements. This regulation includes requirements that are related to the methods used in, the facilities and controls used for, designing, manufacturing, packaging, labeling, installing, and servicing of medical devices that are intended for human use.
The Quality system regulation applies to finished medical device manufacturers who intend to commercially distribute devices. As the QS regulation covers a broader spectrum of devices, production processes, etc., It allows some leeway for manufacturers to determine the necessity for, or extent of, quality elements and to develop and implement specific procedures customized to their specific processes and devices.
Currently, the FDA published a proposed regulation, to amend the device current Good Manufacturing Practice (GMP) requirements of the Quality System (QS) regulation (21 CFR Part 820) to absorb the international standard specific for medical device quality management systems set by the ISO, ISO 13485:2016 Medical devices – Quality management systems – Requirements for regulatory purposes.
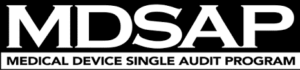
- Therapeutic Goods Administration of Australia,
- Brazil’s Agência Nacional de Vigilância Sanitária,
- Health Canada,
- Japan’s Ministry of Health, Labour and Welfare, and the Japanese Pharmaceuticals and Medical Devices Agency, and
- U.S. Food and Drug Administration
With the advancement of medical device technology in the healthcare industry, Software as a Medical Device (SaMD) has proven its advantage in multiple areas such as monitoring, screening, diagnosis, disease management and therapeutics. SaMD is defined as “software intended to be used for one or more medical purposes that perform these purposes without being part of a hardware medical device” by the International Medical Device Regulators Forum (IMDRF) Software as a Medical Device Working Group. To be considered as a SaMD, the product/device should meet the definition of a medical device first. Some of the examples of the devices which fall under the SaMD category are:
- Software in-vitro diagnostic (IVD) medical device
- Software with a medical purpose that can run on a general-purpose computing platform
- Software for medical image analysis, processing,agement and dose tracking.
SaMD is regulated just like any other traditional medical device depending on country specific regulatory requirements. Regulations are country specific and may differ but to fulfil multiple countries regulatory requirements that are applicable to SaMD, it is recommended to comply with the ISO 13485:2016 and IEC 62304:2006 which is an international standard required by various countries regulatory requirements to market software medical devices including SaMD.
SaMD is regulated just like any other traditional medical device and require a Quality Management System complying with ISO 13485:2016 and fulfilling the requirements of IEC 62304:2006 Medical device software – Software life cycle processes, to market medical device software.